In the field of robotics, precise and reliable force measurement is crucial for achieving accurate control and interaction with the environment. Force sensors, also known as load sensors or force transducers, play a vital role in enabling robots to sense and respond appropriately to external forces. In this blog post, we will explore the application of force sensors in robotics and discuss their significance in enhancing the capabilities and safety of robotic systems.
1. Force Sensing in Manipulation:
Load cells are widely used in robotic manipulation tasks, where robots are required to interact delicately with objects. By integrating force sensors into robot grippers or end-effectors, robots can apply the appropriate amount of force during grasping, lifting, and manipulation tasks. This allows for precise control and prevents excessive force that may damage objects or cause safety hazards.
2. Force Feedback and Compliance:
Force sensors enable robots to provide force feedback, allowing them to perceive the level of force being applied to objects or surfaces. With this feedback, robots can adjust their actions to accommodate varying conditions or achieve a desired level of compliance. For example, force sensors can be used in collaborative robots (cobots) to detect human contact and ensure safe interactions by adapting their movements based on the applied force.
3. Contact Sensing and Object Recognition:
Force sensors integrated into the robot's limbs or fingers can detect contact forces, enabling robots to detect and recognize objects. By analyzing the distribution and magnitude of forces during contact, robots can identify object features and adapt their manipulation strategies accordingly. This capability is particularly valuable in applications such as object sorting, assembly, and tactile exploration.
4. Grasp Force Control:
Force sensors play a critical role in grasp force control, allowing robots to achieve optimal and stable grasping. By continuously monitoring the force exerted on an object during a grasp, robots can adjust their grip to prevent slippage or excessive force. This improves the efficiency and success rate of grasping tasks, especially when dealing with delicate or irregularly shaped objects.
5. Force-Based Compliance Control:
Force sensors enable robots to achieve adaptive control and compliance in various tasks. By measuring the external forces acting on the robot, it can actively adjust its motion and stiffness to interact with the environment accurately. This capability is highly valuable in applications such as compliant assembly, force-sensitive manipulation, and tasks requiring close physical interaction with humans.
Force sensors are indispensable components in the field of robotics, enabling robots to perceive and respond to external forces for enhanced control and interaction. From manipulation and grasp force control to contact sensing and compliance, force sensors contribute to the safety, accuracy, and versatility of robotic systems. As robotics continues to advance, the application of force sensors will play an increasingly significant role in expanding the capabilities of robots and facilitating their into various industries.
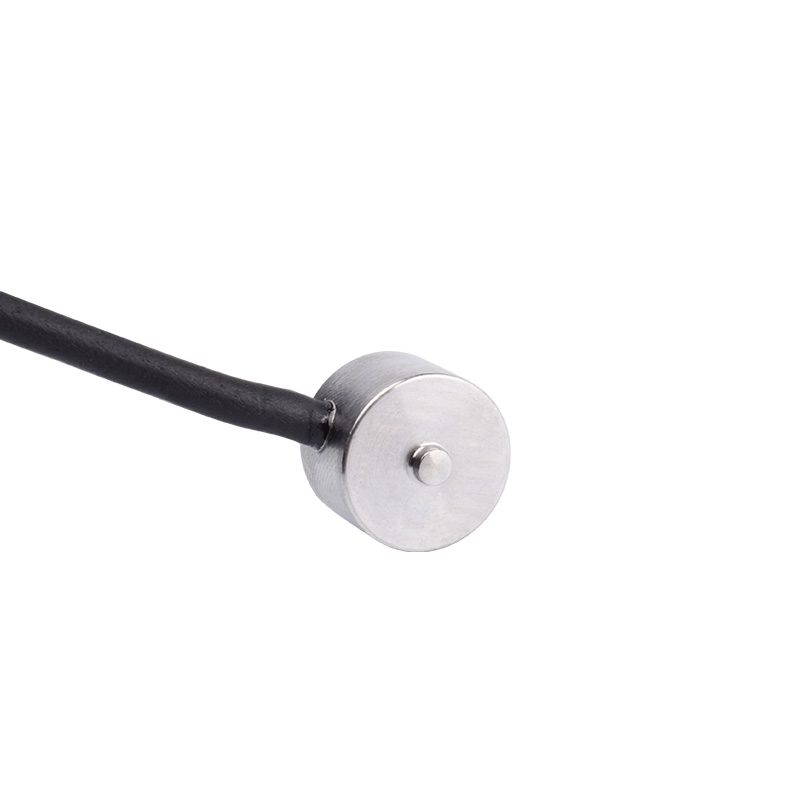