EVA Rubber Technical Insights for Modern Manufacturing
Welcome to the World of Advanced Rubber Engineering
As a leading Chinese rubber supplier, Hairui Rubber understands that behind every industrial material lies a fascinating story of innovation and precision. Today, we're diving deep into the world of Ethylene-Vinyl Acetate (EVA) rubber – a material that quietly powers countless technologies around us.
Why EVA Matters in Modern Manufacturing
Imagine a material so versatile it can be found in everything from comfortable shoe soles to sophisticated electrical cables. That's EVA rubber – the unsung hero of industrial design and engineering.
Fundamental Composition Technical Insights
The Molecular Magic of EVA
For our fellow EVA foam manufacturers and engineering enthusiasts, here's a breakdown that goes beyond basic specifications:
- Vinyl Acetate Content: Precisely 45%
- Density: A robust 980 kg/m³
- Mooney Viscosity: Flexibly ranging 8-16 ML-4
Why These Numbers Matter
These aren't just random figures – they represent the engineering prowess that makes EVA a go-to solution for:
- Mechanical component design
- Advanced adhesive systems
- Specialized cable insulation
A Closer Look At Specialized Rubber Variants
Levapren Series Decoding the Codes
At Hairui Rubber, we pride ourselves on understanding the nuanced world of rubber variants:
- Levapren 452: The versatile mixer
- Complete solubility in multiple solvents
- Ideal for complex compound applications
- KA 8052: The precision specialist
- Partial solubility
- High gel content for specific industrial needs
Thermal Performance The Real-World Test
How Rubbers Survive Extreme Conditions
Let's break down how different rubbers perform under pressure:
- EPDM Rubber
- Thermal Aging Champions
- Maintains strength at 150°C
- Strategic antioxidant integration (Pb304)
- Butyl Rubber (IIR)
- More susceptible to thermal stress
- Demonstrates performance limitations
The Blending Art Industrial Alchemy
As a sophisticated Chinese rubber supplier, we understand that rubber performance is about strategic combinations:
- EPDM + NBR: Enhanced ozone resistance
- Levapren 452: Designed for optimal mixing
- Precise vulcanization rate matching
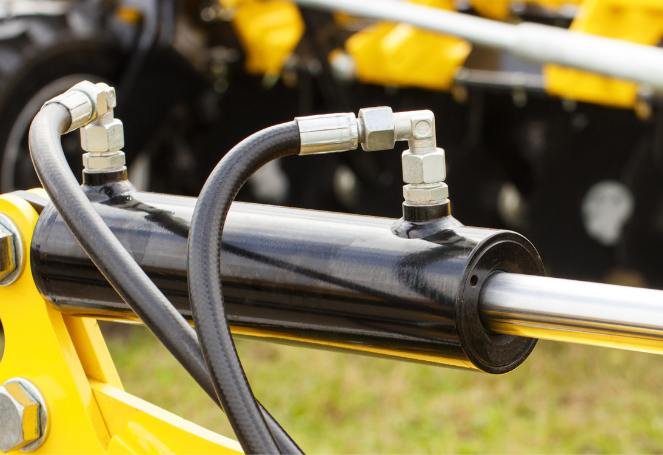
Application Domains
Industry-Specific Rubber Solutions
EVA Applications
- Cable industry insulation
- Specialized textile manufacturing
- Low-viscosity product engineering
EPDM Applications
- High-voltage cable sheaths
- Extreme weather-resistant components
Processing Considerations
Why Processing Matters
For EVA foam manufacturers, these details are crucial:
- Ash content: Minimal 1%
- Volatile components: Less than 0.7%
- Processing stability is key
Alternative Perspectives: Guayule Rubber
A unique natural alternative with:
- Biological source
- High extraction costs
- Strategic emergency resource
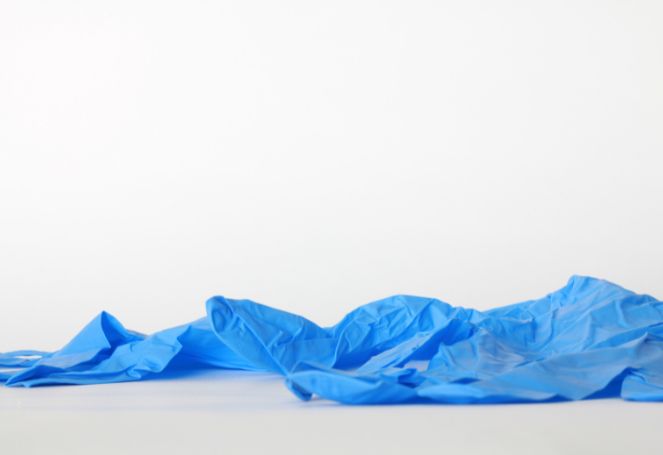
Making the Right Material Choice
Selection Framework for Engineering Professionals
Critical evaluation parameters:
- Specific operating conditions
- Material property requirements
- Environmental constraints
- Temperature tolerance
- Co-vulcanization potential
Final Thoughts on EVA Rubber Innovations
Ethylene-Vinyl Acetate (EVA) rubber represents a pinnacle of material engineering, offering exceptional versatility across industries demanding high-performance, adaptable solutions. From electrical insulation to mechanical components, EVA's unique molecular structure continues to push the boundaries of what's possible in modern manufacturing.
The true strength of EVA lies not just in its technical specifications, but in its ability to solve complex engineering challenges. While other materials may falter under extreme conditions, EVA demonstrates remarkable resilience and adaptability.
Hairui Rubber Commitment
As a leading Chinese rubber supplier, Hairui Rubber is dedicated to delivering EVA rubber solutions that meet the most demanding industrial requirements. Our expertise transforms technical challenges into innovative opportunities.
Discover the Hairui Difference – Precision. Performance. Possibility.
Check the "About Us" page to learn more about Hairui Rubber's values and services.