When it comes to lifting heavy loads and ensuring workplace safety, it's essential to choose the right lifting equipment. Two popular options for material handling in various industries are webbing slings and round slings. While both serve the same purpose, they have distinct characteristics that make them suitable for different applications. In this blog post, we will explore the differences between webbing slings and round slings, highlighting their unique features and common uses.
Round Slings:
Round slings, as the name suggests, are circular in shape and typically made of synthetic fibers like polyester. They feature a continuous loop construction and have no fixed endpoints, providing flexibility in load attachment points. Round slings are known for their excellent strength-to-weight ratio and versatility in handling a wide range of loads.
Key Features of Round Slings:
Soft and non-damaging: The soft texture of round slings minimizes the risk of scratches or dents on delicate surfaces.
High strength: Round slings are designed to withstand heavy loads and offer a high lifting capacity.
Adaptability: The endless loop construction allows for easy adjustment of the sling length to suit different load sizes and shapes.
Load distribution: Round slings evenly distribute the load weight, reducing the risk of damage to the load.
Safety features: Round slings are often color-coded based on their load capacity, ensuring proper selection for each lifting task.
Common Applications of Round Slings:
Rigging and lifting heavy machinery in industrial settings.
Lifting and transporting construction materials.
Offshore and maritime operations.
Tree removal and arboriculture.
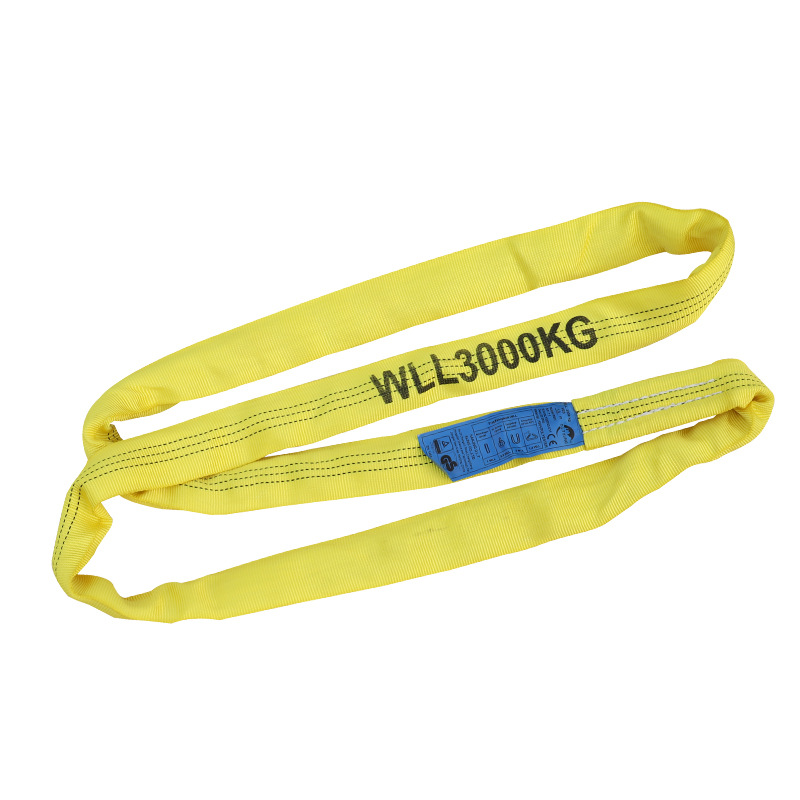
Webbing Slings:
Webbing slings are made of woven polyester or nylon fibers, creating a durable and flexible lifting strap. They have a flat, ribbon-like appearance and come in various widths and load capacities. The most common types of webbing slings include flat eye, twisted eye, and endless loop configurations.
Key Features of Webbing Slings:
Lighter weight: Compared to round slings, webbing slings tend to be lighter, making them easier to handle and transport.
Protection against abrasion: The smooth surface of webbing slings helps minimize damage to delicate or fragile loads.
-Cost-effective: Webbing slings are generally more affordable than round slings, making them a popular choice for light to medium-duty lifting tasks.
Enhanced visibility: Webbing slings are often available in bright colors, enhancing visibility during lifting operations.
Excellent flexibility: Webbing slings offer high flexibility, making them ideal for lifting irregularly shaped loads.
Common Applications of Webbing Slings:
Lifting machinery and equipment in manufacturing and construction industries.
Moving goods in warehouses and logistics operations.
Hoisting materials during maintenance and repair processes.
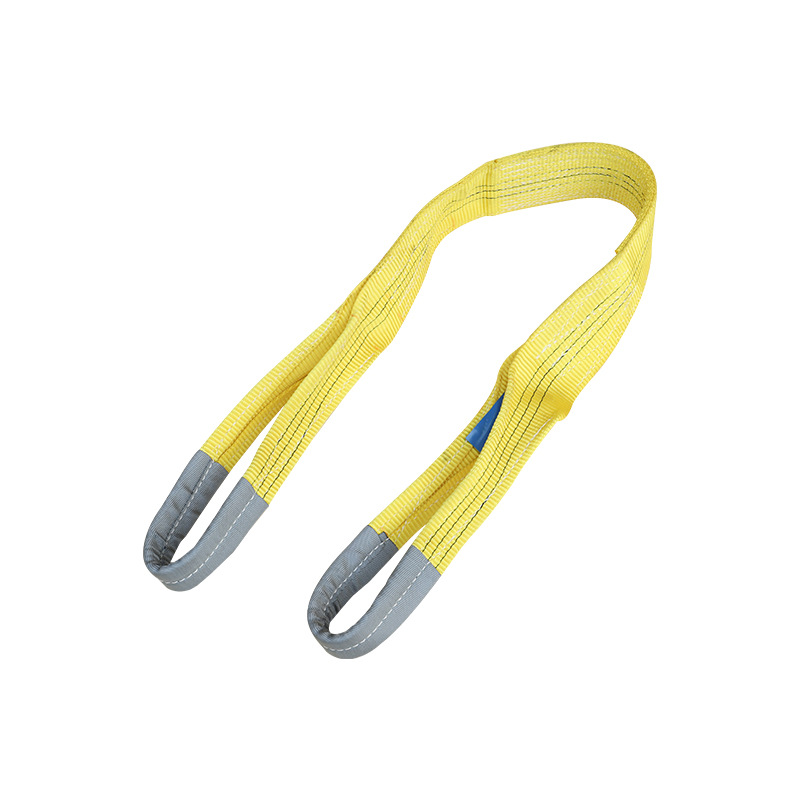
In summary, both webbing slings and round slings serve as crucial lifting tools in a wide range of industries. While webbing slings are preferred for their flexibility, lightweight design, and cost-effectiveness, round slings excel in load distribution, strength, and adaptability. Understanding the differences between these two types of slings is essential to make an informed choice based on specific lifting requirements. Always prioritize safety and compliance with industry standards when selecting and using lifting equipment.